Signs That Your Power Tools Need Repaired or Replaced
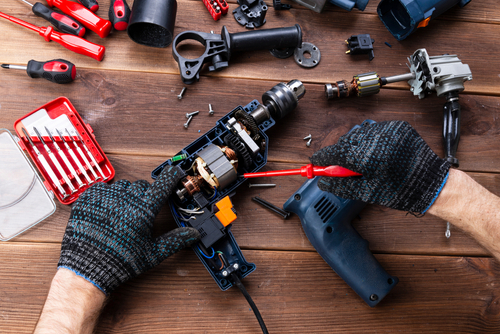
Power tools are an essential part of any handyman or DIY enthusiast’s toolkit. Whether you use them for woodworking, home repairs, or construction projects, it’s important to keep your power tools in good working condition to ensure safety and efficiency. However, over time, these tools can experience wear and tear, leading to decreased performance or even potential hazards. In this blog post, we will discuss some common signs that indicate your power tools may need repairs or replacement.
1. Loss of power or decreased performance
One of the most noticeable signs that your power tool needs attention is a loss of power or a significant decrease in performance. For example, if your drill was once powerful but now struggles to drill through even the simplest materials, it may indicate a problem with the motor or gearbox. Similarly, if your saw is no longer able to cut through wood smoothly and quickly, it may be time to have it repaired or replaced. Loss of power and decreased performance can be a result of worn-out parts or internal damage that needs professional attention.
2. Unusual noises or vibrations
Power tools that produce unusual noises or excessive vibrations often indicate underlying issues. If your power tool is making grinding, squealing, or knocking sounds, it may be a sign of worn-out bearings, loose parts, or damaged gears. Excessive vibrations can also be a cause for concern and indicate imbalance or misalignment. Ignoring these warning signs can lead to further damage and potential safety hazards, so it’s important to have your power tool inspected and repaired by a professional if you notice any unusual noises or vibrations.
3. Overheating or excessive heat generation
Power tools are designed to withstand prolonged use, but if you notice your tool becoming excessively hot during operation, it’s a cause for concern. Overheating can damage the internal components of your power tool and, in extreme cases, even lead to a fire hazard. Common causes of overheating include dust or debris clogging the ventilation system, a faulty motor, or an electrical issue. If you experience overheating, it’s crucial to stop using the tool immediately, let it cool down, and have it inspected by a professional before using it again.
4. Damaged power cords or switches
Power cords and switches are vulnerable areas of power tools and can easily become damaged over time. If your power tool’s cord is frayed, has exposed wires or damaged insulation, it poses a significant safety risk. Similarly, if the switch is loose, unresponsive, or difficult to operate, it should be addressed promptly. Using a damaged power cord or switch can result in electrical shock, short circuits, or even electrocution. In such cases, it’s necessary to either repair the cord or switch or replace them altogether to ensure safety during use.
5. Excessive wear and tear on parts
Power tools are subjected to significant stress and strain during use, which can cause wear and tear on various parts. If you notice excessive wear on the cutting blades, drill bits, or sanding pads, it may be an indication that those parts need to be replaced. Using worn-out parts can not only affect the performance of your power tool but also compromise the quality of your work. Regularly inspecting and replacing worn parts will help maintain the efficiency and longevity of your power tools.
6. Difficulty in starting or shutting down
If your power tool is difficult or slow to start, it may be a sign of an electrical problem or a worn-out starting mechanism. Additionally, if your tool fails to shut down or experiences a delay in turning off when you release the trigger, it could be an indication of a faulty switch or a malfunctioning electronic component. These issues should be addressed promptly, as they can lead to accidents or damage to the tool if left unattended.
Summary
Regular maintenance and prompt repair or replacement of power tools are essential for smooth and safe operation. By recognizing and addressing these signs of potential problems, you can ensure that your power tools continue to serve you well in all your future projects. Always refer to the manufacturer’s guidelines for maintenance and seek professional help from your local repair shop if you are unsure about repairs or replacements. Happy DIY-ing!
Need a Power Equipment Repair Shop in Bells, TN?
Welcome to Hill’s Repair Shop! We have been locally owned and operated since 1964! In our 58 years, we have dedicated ourselves to providing top-of-the-line sales, service, and repairs for all small engines and equipment. Please give us a call for more information!